Microsoft Dynamics Supply Chain Management-Production Bill of Material Creation
Production Order Management;
The primary responsibility of production order is to manufacture finished goods. The manufacturing process may include Raw-material & semi-finished items, which are included in the bill of materials of finished items.
Following options are available for creating a production order:
Manually by entering information in Production order form
Create Production order from Sales order lines
After creating a production order you have to execute all subsequent steps from estimating to ending:
1- Estimation is the first step in order processing after creating a production order. Estimation determines the quantity and cost of all items and resources, which are required for manufacturing the product.
2- Releasing a production order means to hand it over from the front office to the shop floor. When releasing the order, print the production papers if required. Once production order is actually started set the order status to “Started”.
3- Post the production Journal, Shop floor consumes material and resource capacity. Reporting this consumption requires posting production journals. Posting may be setup automatic or manual.
4- Report as finished & End, once manufacturing is completed for the entire or a partial quantity of the finished product, post a reporting as finished transaction. After posting, the reported quantity of the finished product is available in inventory. Then change the Order status to “End”
Create Production Bill of Material (BOM):
A bill of materials (BOM) primarily is a list of products and quantities. The main purpose of a bill of materials is to determine the components (raw material or parts) of a finished item. In order to make use of a bill of materials in production control, BOM must be approved & active.
To create a bill of material from main menu user will access Product Information Management>Bill of materials & Formulas>Bill of Materials
After clicking on Bill of materials a new window will be opened (Given below). User will click on New from header to create a new BOM. In the Bill of material header BOM number will be automatically filled, Enter the name and choose Site & Item group.
In the Bill of material lines click New to add items. Items are consisting of Raw materials, semi-finished goods inventory. Choose items with variant details (i.e. Size, color etc.) and select Site from where item is going to be picked for consumption, specify the date & quantity required per item per line.
After entering all the item details required in BOM, enable approve button to activate the BOM.
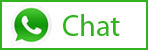
Tags In
Related Posts
Leave a Reply Cancel reply
Categories
- Expense Management Process (1)
- Free In Person Trainings (2)
- Free Microsoft Training Videos on YouTube (13)
- Intensive Microsoft Bootcamps: Learn Fast, Learn Smart (4)
- Life Cycle Services (1)
- Microsoft Dynamics Finance (28)
- Microsoft Dynamics HR & Payroll (4)
- Microsoft Dynamics Supply Chain Management (22)
- Uncategorized (1)